- Home
-
All Categories
- Clothing, Shoes & Jewelry
- Baby
- Kitchen & Dining
- Tools & Home Improvement
- Automotive
- Arts, Crafts & Sewing
- Home & Kitchen
- Sports & Outdoors
- Office Products
- Electronics
- Industrial & Scientific
- Computers & Accessories
- Toys & Games
- Patio, Lawn & Garden
- Pet Supplies
- Grocery & Gourmet Food
- Musical Instruments
- Camera & Photo Products
- Appliances
- Sports Collectibles
- Cell Phones & Accessories
- Video Games
- Health & Household
- Beauty & Personal Care
- Software
- Payment
- About Us
- FAQ
- Privacy Notice
- Shipping & Returns
- Contact Us
Your cart is empty.
Your cart is empty.- Home /
- Automotive /
- Replacement Parts
- Brake System
- Transmission & Drive Train
- Starters & Alternators
- Body & Trim
- Shocks, Struts & Suspension
- Bearings & Seals
- Switches & Relays
- Batteries & Accessories
- Sensors
- Exhaust & Emissions
- Ignition Parts
- Engines & Engine Parts
- Window Regulators & Motors
- Belts, Hoses & Pulleys
- Gaskets
- Fuel System
- Steering System
- Lighting & Electrical
- Engine Cooling & Climate Control
- Windshield Wipers & Parts
- Caps
- Filters
- Motors
- Cables
/
- Body & Trim /
- Body /
- Hoods
Product Description
KW T800 Hood Support Cable Mount Repair Kit
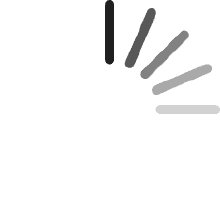
Polyvance's KW T800 hood support cable mount repair kit allows the user to repair the broken, cable mounts on KW T800 Hoods. These hood support cable mounts seem to break easily. Rather than spending thousands on a new hood, Polyvance created the KW T800 Hood Support Cable Mount Repair Kit which repairs and reinforces the broken hood support cable mounts. The cast aluminum cable mounts are screwed and bonded into place with the included PlastiFix high performance methacrylate adhesive. This heavy truck hood repair kit includes the driver and passenger side aluminum castings, 2 kits of PlastiFix adhesive with mixing tips, and screws.
Required Tools and Supplies (not included with kit)
- Adhesive applicator gun and 1001-4 EcoPrep Cleaner
- Medium strength (blue) thread locker
- 90-degree air grinder with 24 to 50 grit roloc sanding discs plus you will need some 60 grit or coarser sandpaper for hand sanding.
- #2 Phillips head screwdriver
- Drill with 5/32" drill bit
- Permanent marker, nitrile gloves, and respirator.
It's easy to install Polyvance's KW T800 hood support cable mount repair kit.
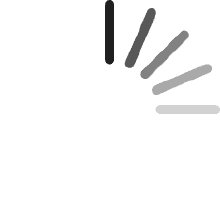
Step 1
Clean the aluminum casting to remove any production oil residue using 1001-4 EcoPrep plastic cleaner (sold separately).
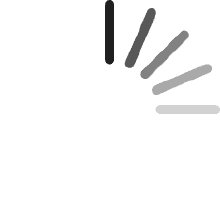
Step 2
Clean the damaged area of the hood with 1001-4 EcoPrep plastic cleaner. Dry completely
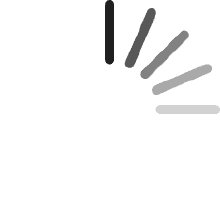
Step 3
Place the casting over damaged area. If the casting doesn’t fit, grind or sand the interference areas of the hood with a Roloc disk or a die grinder.
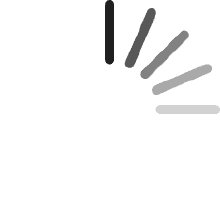
Step 4
Once enough material is removed to roughly fit the casting, trace the outline of the casting using a permanent market.
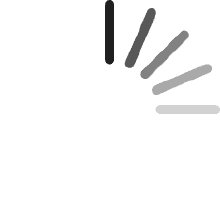
Step 5
Using the outline as a guide, sand the hood until unoxidized raw plastic is exposed. Hand sand inside the pocket with 60 grit or coarser sandpaper.
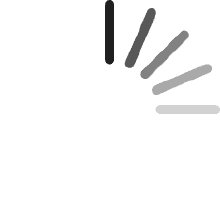
Step 6
Sand the mating surface of casting with a 24 to 50 grit to expose fresh aluminum.
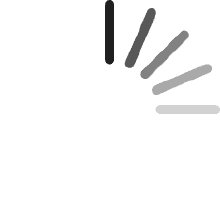
Step 7
Test-fit the casting and grind away any material on the casting or hood to make the two fit. Gaps are acceptable and can be filled with adhesive.
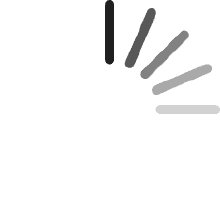
Step 8
With the casting held in place, mark the screw hole locations with a permanent marker.
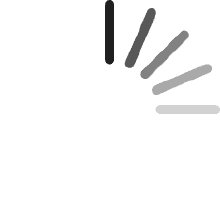
Step 9
Drill the 4 marked places with a 5/32” drill bit. Do not drill through both layers of plastic to the outside of the hood.
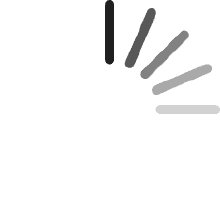
Step 10
Blow away all dust from the sanded surfaces.
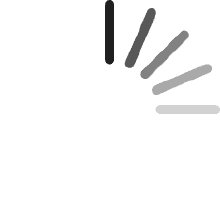
Step 11
Apply about 1/3 of a cartridge of 2510 PlastiFix adhesive to the aluminum casting.
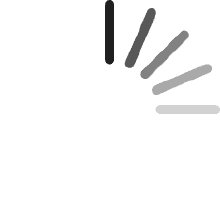
Step 12
Apply approximately 1/3 of a cartridge of 2510 PlastiFix adhesive to the surface of the hood.
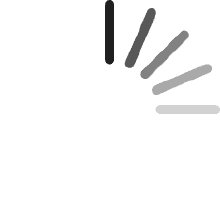
Step 13
Press the casting in place.
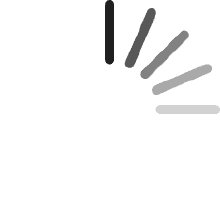
Step 14
Install the (4) screws into the hood. Tighten them evenly until the gaps around the casting are equal.
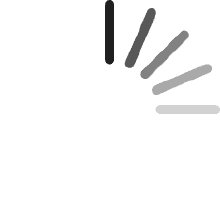
Step 15
Smooth out the adhesive with a gloved finger, forcing excess adhesive into any gaps between the hood and the casting.
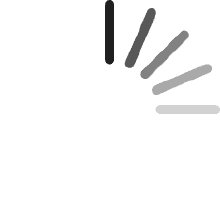
All done
Allow adhesive to cure for 24 hours before attaching the cable.
$39.99 $39.99
$ 18 .99 $18.99
$27.17 $27.17
$ 13 .99 $13.99
$608.99 $608.99
$ 99 .00 $99.00
$35.10 $35.10
$ 15 .99 $15.99
$18.51 $18.51
$ 7 .99 $7.99
$23.49 $23.49
$ 9 .99 $9.99